


WB42: Xr.60-3000
'De naam van de grijper maakt niet zo veel uit, als deze maar pakkend is', Daan van der Lans, 27-09-2016
​
Design fase
Over ons: WB 42

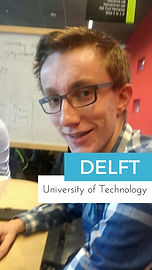
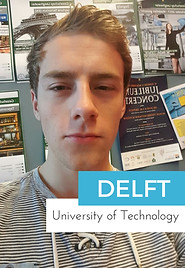

Hoi! Ik ben Justus! Mijn achtergrond als GAMMA goeroe kwam voor ons groepje goed van pas om de essentiële materialen bij elkaar te zoeken en te kopen. Hiernaast probeerde ik op momenten dat het kon zoveel mogelijk humor toe te voegen aan onze groep!
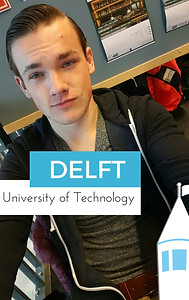
Hallo, ik ben Diego. Samen met deze mensen heb ik gewerkt aan onze grijper, de Xr-60.3000. De uren die we hieraan besteed hebben waren leerzaam en gezellig. Ik ben erg tevreden over de samenwerking binnen deze groep, we konden goed samenwerken en hebben de problemen goed op weten te lossen. We hebben het een uitstekend resultaat behaald.
Hey, ik ben Krijn. De rol die ik binnen dit team speel, is het construeren van deze website. Naast deze fundamentele taak hebben we als team een formidabele grijper als eindresultaat neer weten te zetten.

Hoi ik ben Job, ik vind het erg leuk om dingen te bouwen. Deze grijper was dan ook een leuke uitdaging. Als logo en visual designer ben ik erg tevreden met het uiteindelijke resultaat.
Hoi, ik ben Daan. Ik ben als Matlabmaster een essentiële schakel voor sommigen in de groep. Daarnaast probeer ik me altijd voor ons project in te zetten waar dat mogelijk is.
Hey, ik ben Frank. Samen met een geweldig team hebben wij de Xr.60-3000 ontworpen en gebouwd. Ik ben het artistieke brein achter de film van onze grijper.

Ik ben Denniz! Mijn aandeel in dit project zat voornamelijk in het praktische gedeelte. Ik vond het erg leuk om te bouwen aan de grijper en de benodigde onderdelen uit te zoeken.
Programma eisen& wensen
Opzet programma van eisen en wensen
We begonnen ons project door na te denken over oplossingen voor de problemen.
De grijper die we moesten maken moest een beker, een tetrapak van een halve liter, en een half liter flesje vast kunnen pakken, 15 cm op kunnen tillen,10 cm opzij kunnen bewegen en het voorwerp dan neerzetten op een verhoging. Daarna moet de grijper weer terug naar de rusttoestand.

Om deze uitdagingen aan te pakken hebben we met zijn alle ideeën bedacht voor elk onderdeel van de grijper. We hebben de grijper onderverdeeld in drie delen: de zijwaartse beweging, beweging omhoog/omlaag, het mechanisme van de grijper, de manier van grip, de manier waarop we de beweging geleidelijk laten verlopen en de vorm van de grijper.
Voor elk onderdeel hebben we ideeën bedacht, deze ideeën hebben we in een schema gezet. Deze ideeën hebben we beoordeeld op:
-
De extra kosten voor de grijper zijn minimaal.
-
De grijper kan gemakkelijk aan het systeembord bevestigd worden en klaargemaakt worden om te functioneren (snel actuatoren kunnen inbouwen in de grijper).
-
De onderdelen moeten sterk genoeg zijn om de last te dragen.
De uiteindelijke keuzes hebben we uitgewerkt, en waar nodig aangepast. We hebben bijvoorbeeld de afstand waar de actuator op de rails is bevestigd aangepast zodat de
beweging van de arm omhoog minder kracht kost.
Prototype
Tekenen
Bouwen
Voor dat we onze grijper konden bouwen moesten we natuurlijk eerst een grijper ontwerpen. zo heeft iedereen een design gemaakt en vervolgens hebben we bekeken welke het beste was. het ontwerp wat we hebben gekozen hebben we later nog iets aangepast. het voordeel van het gekozen ontwerp is dat het vrij gemakkelijk werkt en ook makkelijk was om het daadwerkelijk te maken. een nadeel, en ook een probleem waar we pas later tegenaan kwamen, is dat de grijparm het flesje zou omstoten als we hem horizontaal zouden bewegen. gelukkig hebben we dit probleem opgelost door de horizontale beweging de andere kant op de doen.
​
​
​
​
​
​
​
​
​
​
​
​
​
​
​
​
​
​
​
​
bij het bouwen van de grijper hebben we gebruikt gemaakt van diverse materialen. zo konden we acryllen onderdelen laten maken met de specifieke afmetingen van ons ontwerp. ook hebben we gebruik gemaakt van hout en zelfs een spons. doordat de onderdelen voor ons gemaakt werden hebben we de grijper in elkaar kunnen zetten als een soort bouwpakket met hier en daar wat improvisatie.


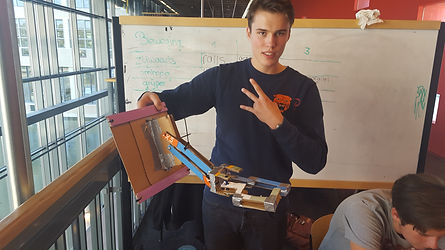
Fabricage onderdelen
De Xr-60.3000 bestaat hoofdzakelijk uit twee materialen, namelijk hout en perspex. Vanuit de faculteit werd ons de mogelijkheid geboden om een beperkte hoeveelheid perspex te laten lasersnijden. De houten onderdelen hebben we allemaal zelf gezaagd.
Perspex
Hout
Perspex heeft als materiaal een aantal belangrijke voordelen, zo ook bij de fabricage van onze grijper. Ten eerste is het relatief licht, waardoor we de kracht van de actuatoren besparen. Verder is het ook makkelijk te verwerken, we hadden natuurlijk al het voordeel dat de gaten voor de bouten al gesneden werden, maar we kwamen erachter dat zelf gaten boren in het perspex een koud kunstje is.
Naast de geleverde perspex zijn er nog een paar onderdelen die we van hout hebben gefabriceerd. De voordelen van hout tegenover perspex zijn vooral dat hout makkelijk te verschaffen en te vervaardigen is. Een bezoekje aan de bouwmarkt voorzag ons van de nodige hoeveelheid hout, wat we vervolgens doormiddel van een handzaag in de gewenste vormen kregen. Bijvoorbeeld de plaat waar de rails aan vast zit, het blok dat aan de wieltjes van de rails vast zit, en het blok tussen de arm en de grijper zelf, zijn allemaal van hout gefabriceerd, met als hoofdreden, dat perspex niet geschikt is om bijvoorbeeld een blok van te maken.

Elastiek
Ook hebben we elastiek gebruikt voor de grijper, zowel om de druk te verlagen waardoor de grijper minder harde en snelle bewegingen zou maken, als om op de stilstaande armen meer wrijving toe te voegen tussen de stilstaande armen en het object door elastiek om de armen heen te wikkelen.

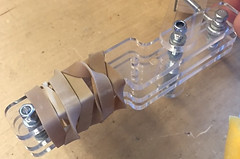
Rails met wieltjes
​Om de horizontale beweging te realiseren hebben we gekozen om een rails te maken op een plank hout, waartussen de grijper kan bewegen door wieltjes tussen de rails te plaatsen en de actuator vast te maken aan de grijper en vervolgens te laten in- en uitschuiven.
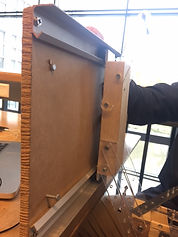
Spons
Om de armen van de grijper van meer wrijving te voorzien tussen de armen en het flesje/bekertje/tetra pak, hebben we gekozen om spons tussen de perspex lagen van de armen te stoppen. Hierdoor wilden we voorkomen dat de het flesje/bekertje/tetra pak door de armen naar beneden zou vallen.
Bouwen van de grijper
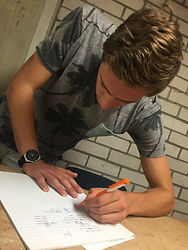
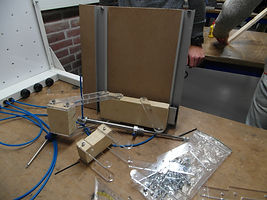
De ‘Xr.60-3000’ work in progress.
Ons avontuur ging van start met het bedenken van technieken om de doelstelling te kunnen halen. Door onze ideeën te combineren zijn we uiteindelijk bij een geweldige combinatie van technieken gekomen die aan al onze verwachtingen zou voldoen. Na wat overleg en de benodigde berekeningen hebben we een tekening gemaakt waarin de exacte specificaties stonden. Om onze perspex onderdelen uit te kunnen snijden hebben we onze specificaties verwerkt in een ‘Solidworks’ tekening. Eenmaal deze onderdelen ontvangen kwamen we achter het feit dat we in een paar onderdelen gaten voor de bouten waren vergeten. Dit probleem hebben we opgelost door met een boor voorzichtig op de juiste plekken nieuwe gaten te boren. Eerst hebben we ons rail systeem in elkaar gezet, met spullen van de bouwmarkt hebben we een perfect werkende rails weten te maken. Vervolgens hebben we de grijparm en de vingers van de grijper in elkaar gezet. Uiteindelijk hebben we alles in elkaar gezet en was ons idee werkelijkheid geworden, nu was het moment van de waarheid daar, de dag om onze grijper te testen. Nadat we de actuatoren op onze grijper hadden bevestigd steeg de spanning enorm bij onze groepsleden, gelukkig verliep de test uitstekend.

De grijper: 'Xr.60-3000'
De Xr-60.3000 is een robuust ontwerp, dat al de vereiste taken goed en naar verwachtingen kan uitvoeren. Hieronder zijn alle bewegingsmogelijkheden van de grijper grafisch weergegeven. Daarnaast vind je onderaan de pagina een filmpje over ons project, waarin je een korte inkijk krijgt in het proces dat wij zijn doorlopen om tot ons eindproduct te komen. De grijper is vrijwel volledig geworden hoe we hem in gedachten hadden en dus kijken wij met gepaste trots terug op een geslaagd project.



Product evaluatie
Zoals in het filmpje te zien is, hebben we aan bijna alle taken voldaan. Het enige dingetje is dat we niet voor elkaar hebben gekregen dat de grijper geleidelijk aan bewoog en niet abrupt stopte. Dit hebben we wel geprobeerd door elastieken aan de armen toe te voegen van de grijper, maar dit hielp niet volledig. Ook hebben we de druk wat lager gezet, maar nog steeds mocht het niet baten. Probleem was voornamelijk dat de opwaartse beweging meer kracht nodig had dan de andere bewegingen, waardoor de andere bewegingen nog steeds te hard gingen en abrupt tot stilstand kwamen.
​
Daarnaast hadden we vooraf beredeneerd dat de grijper tot ongeveer 17 cm hoogte zou komen in zijn hoogste stand. In de praktijk bleek dit echter slechts rond de 15 cm te komen. Gelukkig beïnvloedt dit de werking van de grijper nauwelijks. We denken dat dit verschil te wijten is aan speling in de scharnieren van de grijper en minimale mispositioneringen van sommige onderdelen die bij elkaar tot een grotere afwijking kunnen leiden.
Proces evaluatie
Het proces verliep over het algemeen vrij soepel. Tijdens het hele project hielden we ons goed aan de deadlines, waardoor we over het algemeen goed op schema liepen. Ook hebben we geleerd dat het aanstellen van een notulist en een voorzitter ons erg heeft geholpen om een effectieve manier van werken te vinden. In de eerste weken hielden we ons nog niet zo goed aan deze structuur, maar dit ging gaandeweg steeds beter.
Desondanks waren er enkele problemen waar we tegenaan zijn gelopen. Een voorbeeld van zo'n probleem was het vergeten van het tekenen van een paar gaten in de Solidworks file voor het lasersnijden van de perspex plaat. Dit hebben we gelukkig, net als andere kleine problemen, makkelijk kunnen verhelpen zonder te hoeven ingrijpen in het ontwerp van onze grijper.